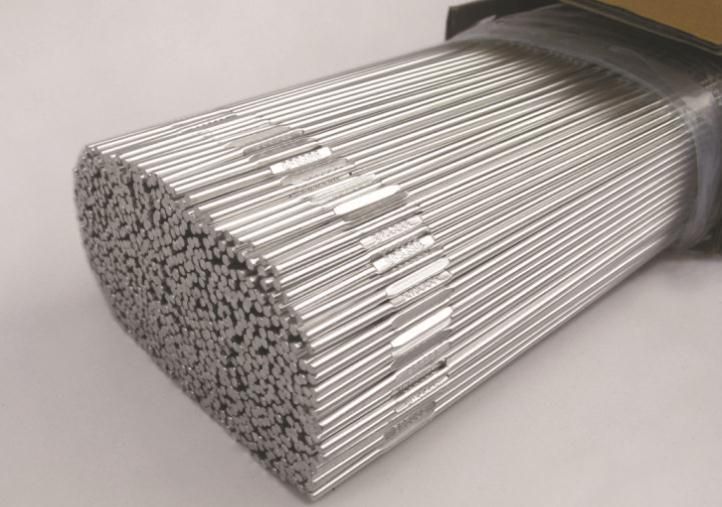
Stainless steel electrode
November 20, 2021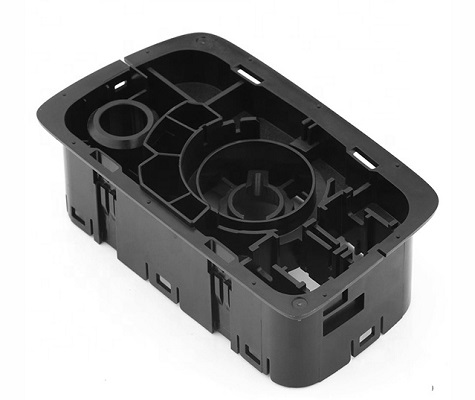
Custom Plastic Injection Molding
December 10, 2021Basic knowledge of sheet metal parts
Sheet metal overview
Sheet metal parts are products processed by sheet metal technology. Sheet metal parts are produced by filament power winding, laser cutting, heavy processing, metal bonding, metal drawing, plasma cutting, precision welding, roll forming, sheet metal bending, die forging, water jet cutting, and precision welding. .
Sheet metal definition: Sheet metal is a comprehensive cold working process for metal sheets (usually below 6mm), including shearing, punching/cutting/compounding, folding, welding, riveting, splicing, forming (such as car body), etc. Its notable feature is the same thickness of the same part.
Sheet metal features
Sheet metal parts have the characteristics of light weight, high strength, electrical conductivity (can be used for electromagnetic shielding), low cost, and good mass production performance. They have been widely used in electronic appliances, communications, automotive industry, medical equipment and other fields, such as In computer cases, mobile phones, and MP3, sheet metal parts are an indispensable part.
As the application of sheet metal becomes more and more extensive, the design of sheet metal parts has become a very important part of the product development process. Mechanical engineers must be proficient in the design skills of sheet metal parts, so that the designed sheet metal meets the product requirements. The requirements of function and appearance can make the stamping die manufacturing simple and low cost.
Sheet metal materials
There are many sheet metal materials suitable for stamping processing. Sheet metal materials widely used in the electronic and electrical industry include:
1. Ordinary cold rolled plate SPCC
SPCC refers to the continuous rolling of steel ingots through cold rolling mills into steel coils or sheets of required thickness. There is no protection on the surface of SPCC, and it is easily oxidized when exposed to the air, especially in a humid environment, the oxidation speed is accelerated, and dark red rust appears. The surface should be painted, electroplated or other protections when in use.
2. Galvanized steel sheet SECC
The substrate of SECC is ordinary cold-rolled steel coil, which becomes electro-galvanized product after degreasing, pickling, electroplating and various post-treatment processes on the continuous electro-galvanizing production line. SECC not only has the mechanical properties and similar processability of general cold-rolled steel sheet, but also has superior corrosion resistance and decorative appearance. It is highly competitive and replaceable in the market of electronic products, home appliances and furniture. For example, SECC is commonly used in computer cases.
3. Hot-dip galvanized steel sheet SGCC
Hot-dip galvanized steel coil refers to the semi-finished product after hot-rolling and pickling or cold-rolling, which is cleaned and annealed, and then immersed in a molten zinc bath at a temperature of about 460°C, so that the steel sheet is coated with a zinc layer and then quenched and tempered It is made by leveling and chemical treatment. SGCC material is harder than SECC material, has poor ductility (avoid deep drawing design), thicker zinc layer, and poor electric weldability.
4. Stainless steel SUS301
The content of Cr (chromium) is lower than that of SUS304, and the corrosion resistance is poor, but it can get good tensile force and hardness after cold working, and it has good elasticity. It is mostly used for shrapnel springs and anti-EMI.
5. Stainless steel SUS304
One of the most widely used stainless steels. Because it contains Ni (nickel), it has better corrosion resistance and heat resistance than Cr (chromium) steel. It has very good mechanical properties, no heat treatment hardening phenomenon, and no elasticity.
Sheet metal design
To meet the requirements of the product’s function and appearance, the design of sheet metal parts should ensure simple stamping process, easy stamping die production, high stamping quality of sheet metal parts, and stable dimensions. For detailed sheet metal parts design guidelines, please refer to the “Part Structure Design Processability” and “Product Design Guidelines for Manufacturing and Assembly” published by the Machinery Industry Press.
Sheet metal equipment
Generally speaking, the basic equipment of a sheet metal factory includes Shear Machine, CNC Punching Machine/Laser, Plasma, Waterjet Cutting Machine (Laser, Plasma, Waterjet Cutting Machine)/Combination Machine , Bending Machine and various auxiliary equipment such as: decoiler, leveling machine, deburring machine, spot welding machine, etc.
Processing steps
Generally, the three most important steps in a sheet metal factory are shearing, punching/cutting, and folding.
Sheet metal is sometimes used as a pull metal. Generally, some metal sheets are plastically deformed by hand or die stamping to form the desired shape and size, and can be further welded or a small amount of machinery Processing to form more complex parts, such as chimneys, tin stoves, and car shells commonly used in homes are all sheet metal parts.
Sheet metal processing is called sheet metal processing. Specifically, for example, the use of plates to make chimneys, iron barrels, fuel tanks, oil tanks, ventilation pipes, elbows, elbows, squares, funnels, etc. The main processes are cutting, bending, bending, forming, welding, riveting, etc. Certain geometric knowledge.
Sheet metal parts are thin sheet metal parts, that is, parts that can be processed by stamping, bending, stretching and other means. A general definition is a part with a constant thickness during the processing process. The corresponding is casting parts, forging parts, Machining parts, for example, the outer iron shell of a car is sheet metal, and some kitchen utensils made of stainless steel are also sheet metal.
Sheet metal craft
Modern sheet metal technology includes: filament power winding, laser cutting, heavy processing, metal bonding, metal drawing, plasma cutting, precision welding, roll forming, sheet metal bending, die forging, water jet cutting, precision welding, etc. .
In 3D software, SolidWorks, UG, Pro/E, SolidEdge, TopSolid, etc. all have sheet metal parts, mainly through the editing of 3D graphics to obtain the data required for sheet metal processing (such as unfolded drawings, bending lines, etc.) ) And provide data for CNC Punching Machine/Laser, Plasma, Waterjet Cutting Machine (Laser, Plasma, Waterjet Cutting Machine)/Combination Machine and CNC Bending Machine.